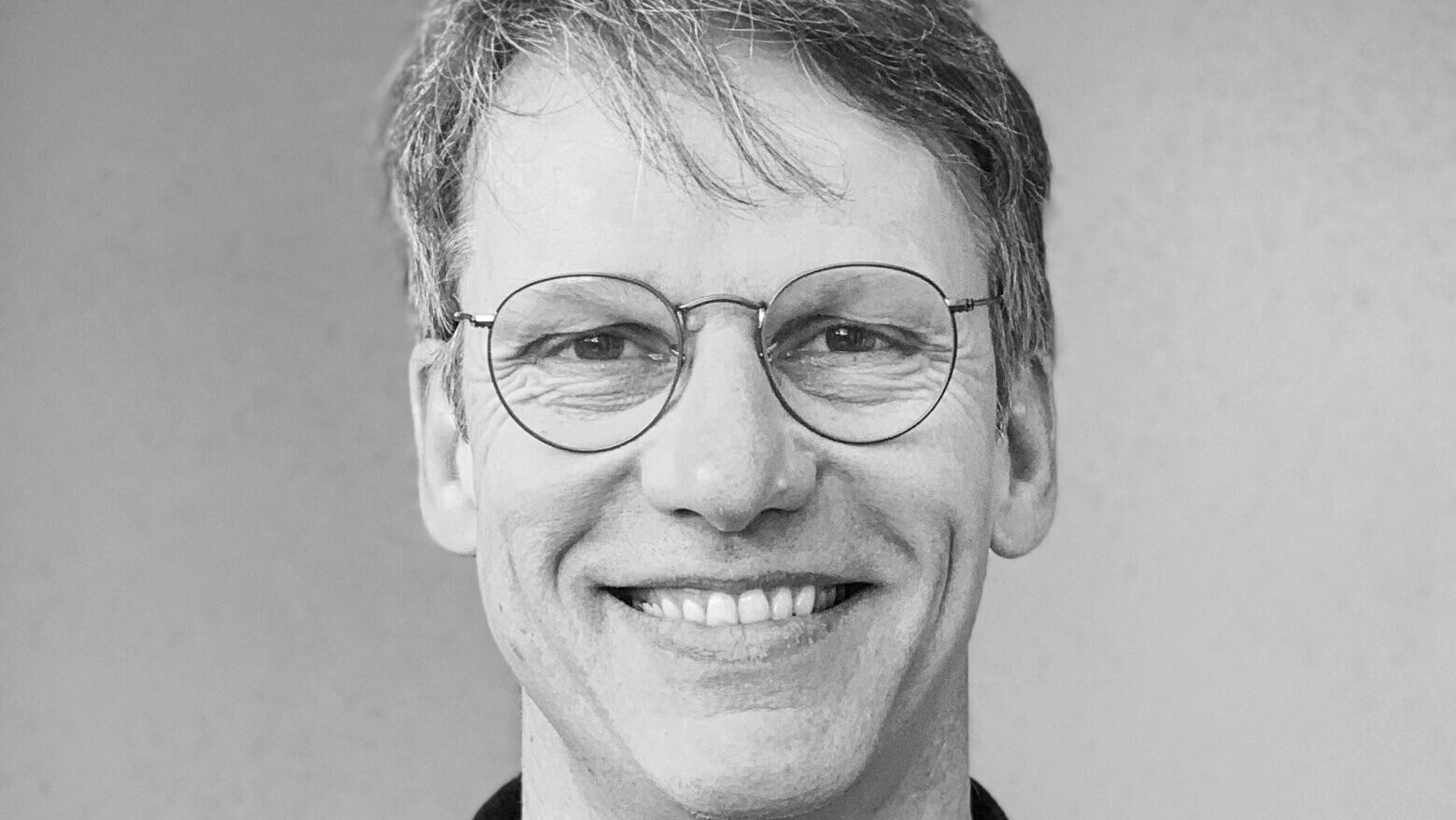
Zeller Kölmel Architekten have been doing architecture for 20 years. In addition to more classic design topics such as urban construction and creating high spatial quality, they deal with social topics such as new forms of living and generally also with sustainable, ecological building. Since they decided to focus on energy efficiency and sustainability parallel to their everyday business 15 years ago, it hardly comes as a surprise that the reconstruction project Saint Stephen’s Church (Stephanuskirche), built in the 1960s, landed in the Cologne-based office and that PREFA also found its way into the project.
“When we build, we create part of our environment. […] It surrounds us like the nature we come from.“
The situation
Köln-Riehl (DE). – An overgrown property with a church which has clearly seen better days. It exhibits two triangular roof surfaces that pointedly run downward from the ridge. There are large overhangs by the glass façades facing southwest and southeast, and underneath, an extensive, powerful glass artwork is hidden behind dull Plexiglas plates. Adjacent to it, a community centre that can no longer keep up with the development of the community. “The building did not have any reconstruction potential, as it was very low and in a poor condition. It is true that you destroy grey energy, but in this case, we decided to go with a new construction that has a sculptural, graphic power and creates an added value for the quarter and its users with additional space, youth rooms, multi-purpose rooms as well as three wheelchair-accessible flats,” recounts Klaus Zeller, who was in charge of the project.
The church could stay, however. “It’s a strong building. The architects Ingeborg Winter-Bracher and Fritz Winter really came up with a great design, as did the artist Lothar Quinte, whose 14 m tall stained glass artwork was preserved and remained in its installed position during the entire reconstruction work,” Zeller tells us. Since this was not a case of monument protection, the building structure could be treated more freely and creatively: “This meant that we could intensify what we valued in the old building and, at the same time, were still able to realise our own design approach. For instance, now that the gallery has been removed, the spectacular space can truly be experienced.”
As lightly as possible
This design approach included covering the roofs of the church and the centre with Prefalz in P.10 dark grey, whose calm colouring harmonises nicely with the other materials in the ensemble. During our conversation, Klaus Zeller draws our attention to the fact that using the same standing seam covering also created a certain formal relationship between the structures. “The top and bottom parts of the two buildings end analogous to one another.” The option to receive all the gutters, pipes and ventilations in the same colour can make a complex decision a little bit easier. The material characteristics of aluminium were also decisive, as the statics of the large steel construction made it necessary to construct as lightly as possible.
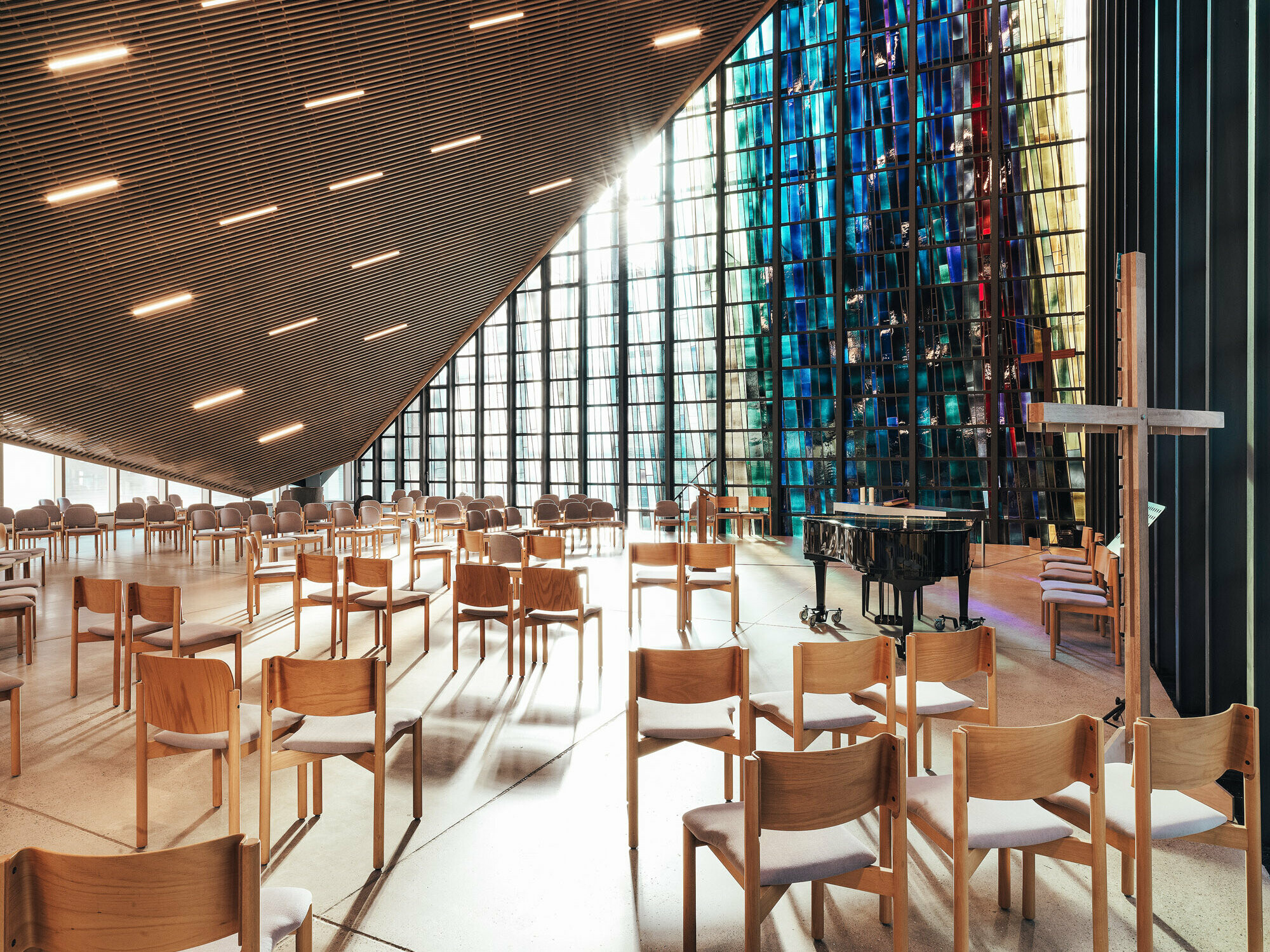
Energy meets art
Since the barely existing insulation made it difficult to use the church building before the reconstruction, Zeller Kölmel Architekten used building simulations to come up with an energy concept that prevented the previous temperature variations between 5 °C and 40 °C and was therefore able to create a pleasant room climate. The architects naturally wanted the artwork to still receive enough sunlight – “because otherwise, it would die” –, but they also wanted to avoid having to use technical cooling: “Given our energy approach, we were adamant about not using air conditioning. We eventually built a second envelope along the roof overhang to thermally use the interspace. This way, the heat that is generated there can be ventilated to the outside before it reaches the interior.”
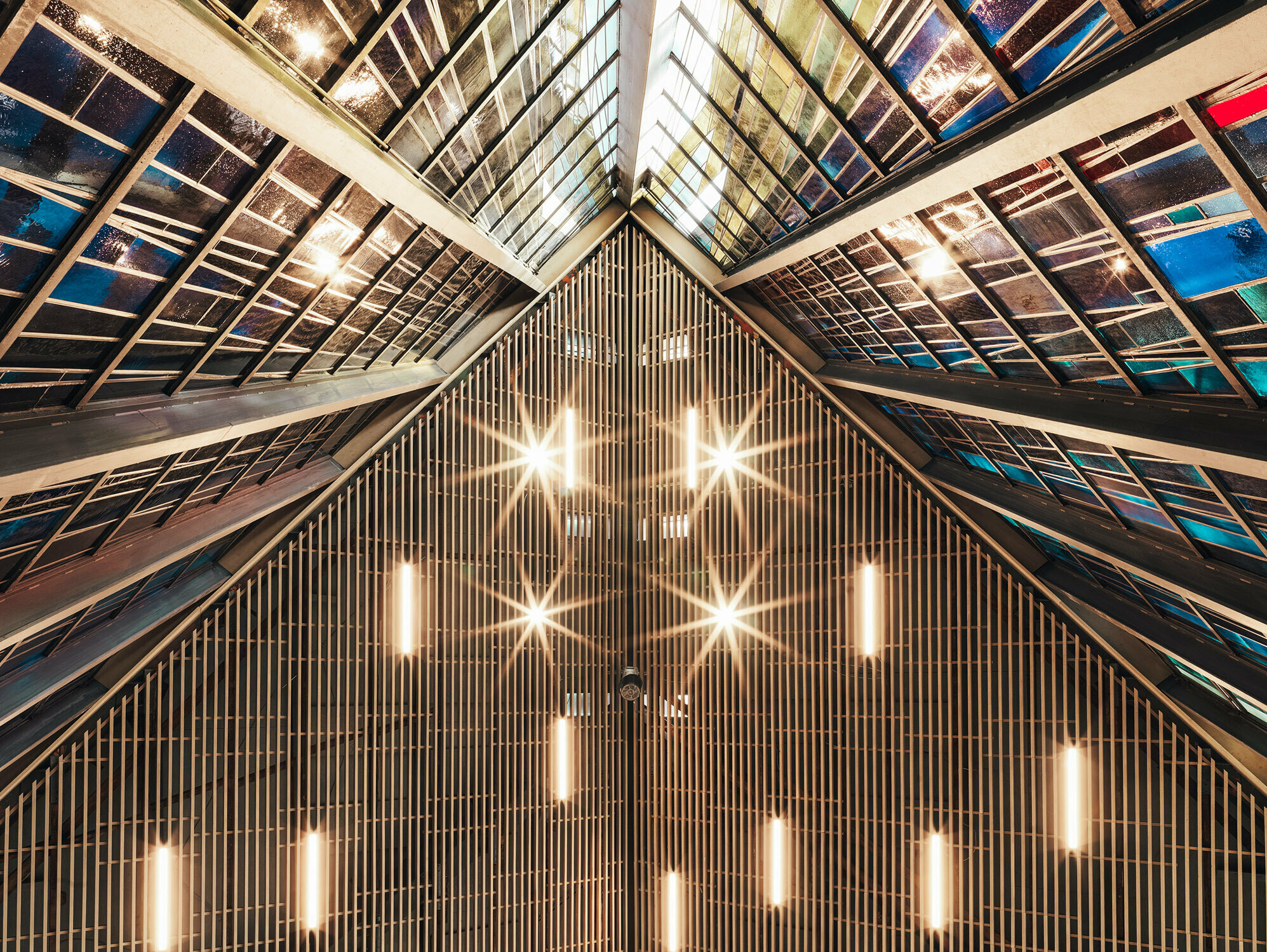
Crystal clear?
AH: “You mentioned that you purposely did not use float glass on the exterior of the triple glazing in order to prevent a ‘reflecting, dematerialised building.’”
KZ: “Exactly, we did not want any form of reflection here. Since the church was hardly noticeable before, we wanted to create something that is corporeal so that it has a larger presence in the city. The structured glass with the broom-finished structure, which was used for the outermost layer of the three glass layers, merely creates a shimmering, not a clear reflection. First, we tested it with small sample panes, and then with six to eight large panes. On the one hand, we wanted the artistic glazing to shimmer through like an inclusion in a crystal. Yet it was also important to us that the sun still has a direct ratio, so that the coloured light of the glazing shines onto the interior and the floor in patches and is not scattered completely.”
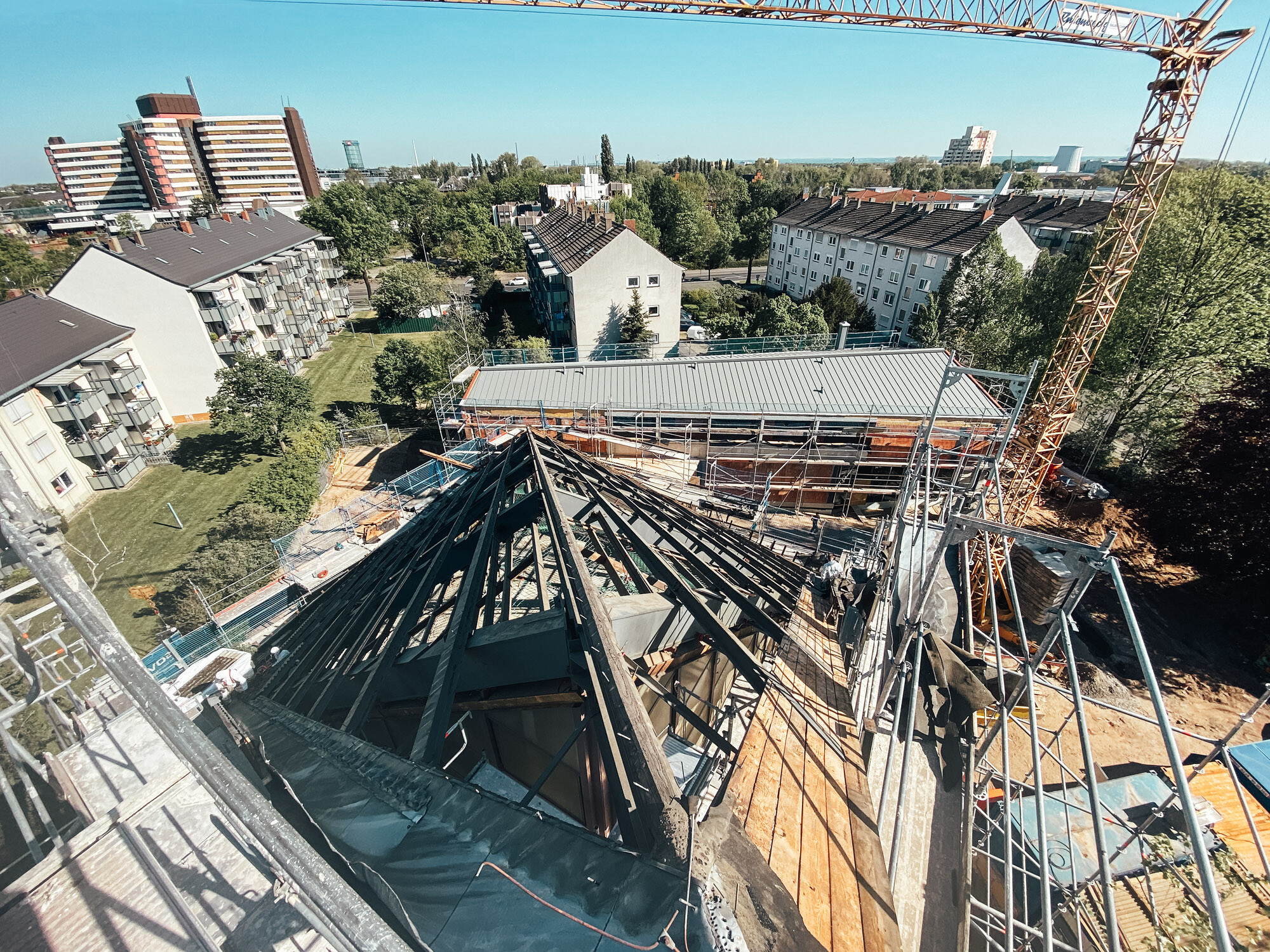
Detailed consultation
The architects already included the tinsmith team of Hoffmann Bedachungen, whom they had worked with several times before, during the pre-planning stage. “It was challenging that the roof geometry created a watercourse that does not run normal to the ridge, meaning that the water flows obliquely towards the standing seams. Moreover, recessed drainage channels which can hold 2 to 3 m³ of water were installed. Due to these circumstances, several covering materials were ruled out from the start, but with PREFA, this was not a problem,” craftsman Sebastian Hoffmann emphasizes. The laying work was carried out over a period of 2 weeks with six tinsmiths continuously on the roof and up to twelve at peak times. “PREFA object consultant Carsten Friedt really gave us excellent advice, particularly regarding the thermal expansion on the steel construction. It was good that we had a consultant who was a master tinsmith,” says Mr. Hoffmann.
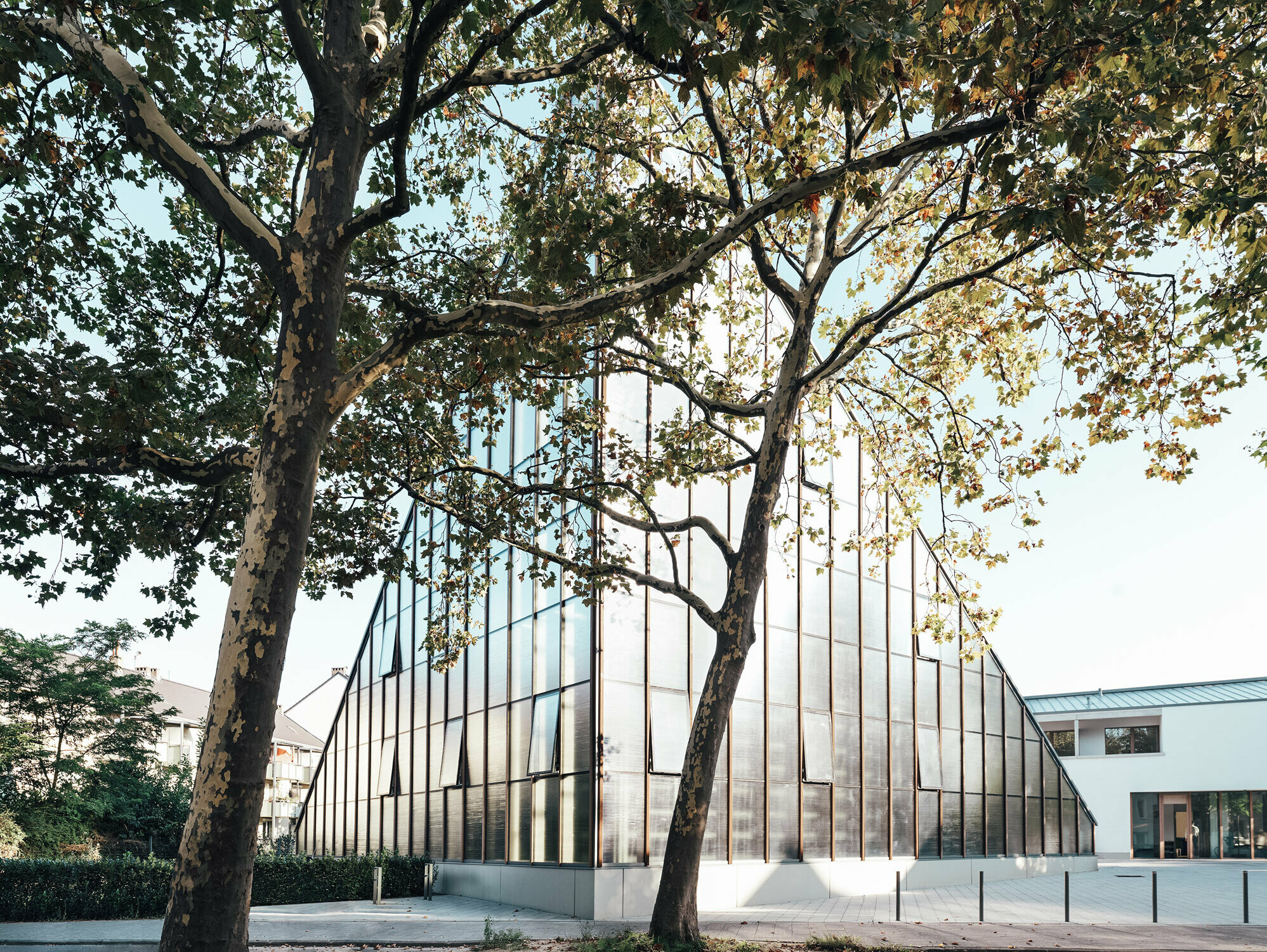
A body is born
If you recall the condition that Saint Stephen’s Church was in before the reconstruction work, it rather resembled a folded plate whose effect had faded over the course of time. Now, it is surrounded by an inviting church square that gives the building a larger presence and exhibits an architectural relationship between the church and the community centre in the ensemble. In Mr. Zeller’s words: “It’s a strong body, the external effect has fundamentally changed. Like a crystal that reveals its colourful, shimmering inclusion in the evening light.”
Saint Stephen’s Church (Stephanuskirche) - details
Country: |
Germany |
Object, location: |
church and community centre, Cologne |
Category: |
reconstruction and new construction |
Architecture: |
Zeller Kölmel Architekten |
Installer: |
Hoffmann Bedachungen |
Material: |
|
Colour: |
P.10 dark grey |
Further information
- Text & interview: Anneliese Heinisch
- Photos: © Nikola Tacevski, Photographer
- Plans & portrait: © Zeller Kölmel Architekten
- Construction site photo: © Hoffmann Bedachungen